3 Ways To Manage Costs and Improve Workforce Planning in the Manufacturing Industry
The manufacturing industry faces uncertainty and a need to innovate. Learn how to use workforce planning to drive investment, skills, and productivity.
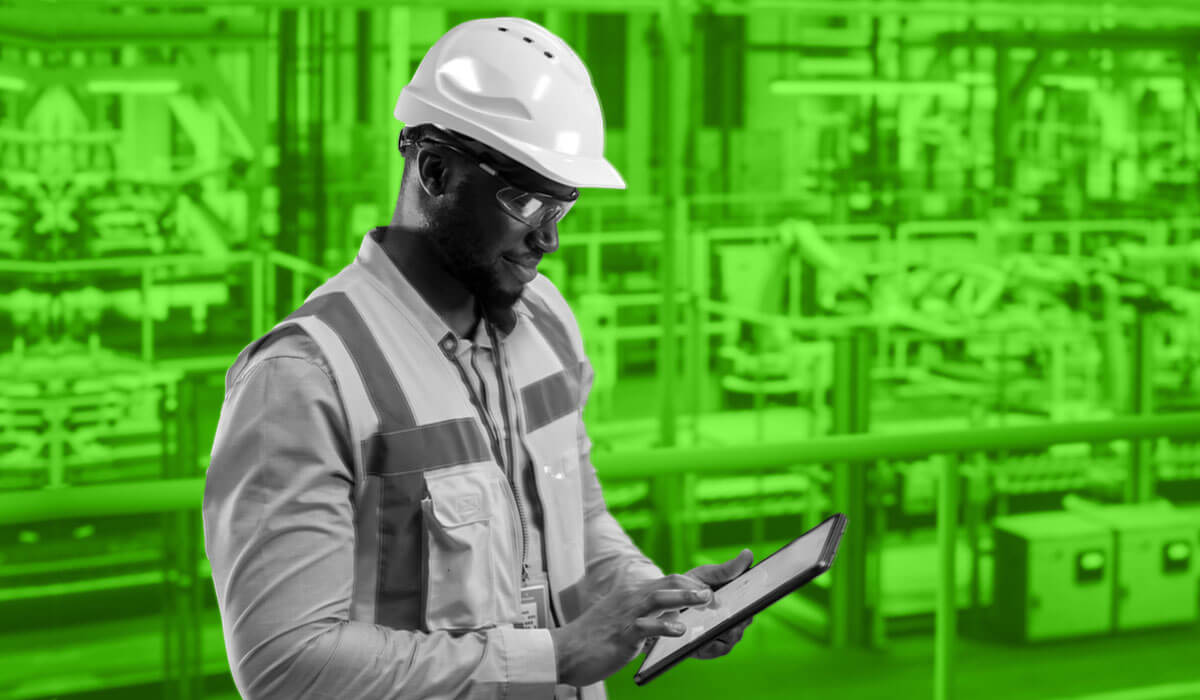
In 2025, the manufacturing industry continues to face a mix of uncertainty and opportunity. Supply chain disruptions, evolving technologies like AI and robotics, and ongoing talent shortages have transformed how manufacturing leaders need to approach workforce planning.
Globally, manufacturers are being asked to do more with less. As reshoring and nearshoring gain traction, businesses must rethink how they invest in their workforce to stay resilient and competitive. The ability to align your people strategy with business goals and outcomes is essential.
Here are three ways workforce analytics can help manufacturing organizations control costs and drive long-term workforce productivity.
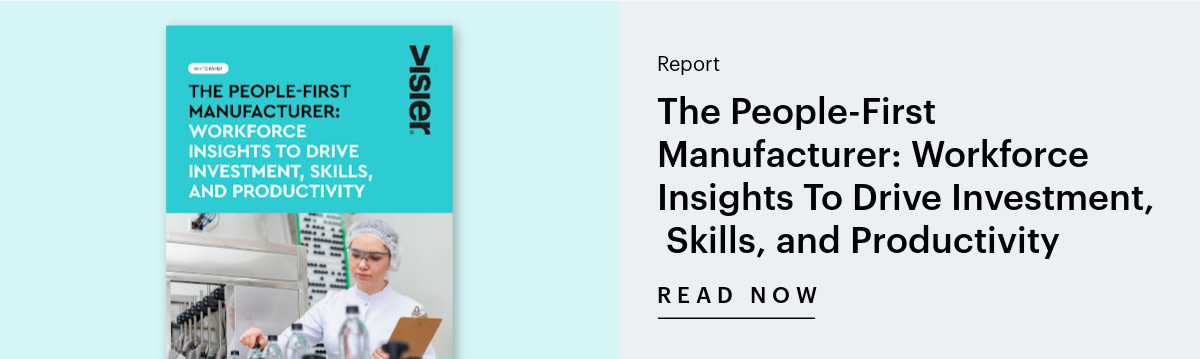
1. Enable strategic workforce conversations with better data
The manufacturing industry faces constant change due to labor shortages, global economic conditions, and technological advancements. To stay competitive, manufacturing leaders must leverage AI and modernize their operations to retain skilled workers in an increasingly competitive—and changing—market.
This requires collaboration between HR, finance, operations, and executive teams to make informed decisions based on a shared understanding of the workforce. That alignment starts with connecting people data and work data.
When everyone has access to trusted workforce insights, it becomes easier to have forward-looking conversations about cost, capacity, and capability. For example:
Are our wages competitive in today ’s labor market across key regions?
What are the current and emerging skills needed for future growth?
Are we investing in training that top talent actually values?
How are we measuring the return on our upskilling efforts?
“People analytics isn't just for HR, it's a business investment. With [Visier] we are able to see the impact of our workforce on our business as our profitability was negatively affected by higher turnover rates.”
Kristi Partlow, Manager, HR Systems & Projects, Printpack
This kind of collaboration is more urgent than ever. According to a Deloitte and The Manufacturing Institute report, the net need for new employees in U.S. manufacturing could reach 3.8 million between 2024 and 2033. 1.9 million of these jobs (50%) could prove hard to fill due to skills shortages in the U.S. manufacturing industry
People analytics platforms help leaders uncover these insights, measure learning impact, and track labor trends in real-time. By connecting the dots across data silos, manufacturers can avoid unnecessary hiring, reduce turnover, and make smarter long-term investments in their workforce.
2. Focus on strategic skills to reduce costs and build agility
Manufacturing companies everywhere are grappling with how to grow while managing tight margins. They need a data-driven understanding of how to best align the right skills to the right roles at any given time.
In an environment shaped by cost pressures, workforce shortages, and technological disruption, organizations must assess not just whether they’re offering training—but whether they’re offering the right training. That means evaluating the depth, relevance, and accessibility of learning and development (L&D) programs across the entire workforce.
“A manufacturing business needs to be able to quickly understand what training activities to invest in and support, and which to cut altogether.”
According to Deloitte, reskilling can be up to six times less expensive than hiring externally. Leading organizations are rethinking traditional learning approaches, embracing digital tools and microlearning, and tying every training initiative to tangible outcomes. Workforce analytics give leaders insights into which candidates are in the best position to reskill and how these actions could impact future success.
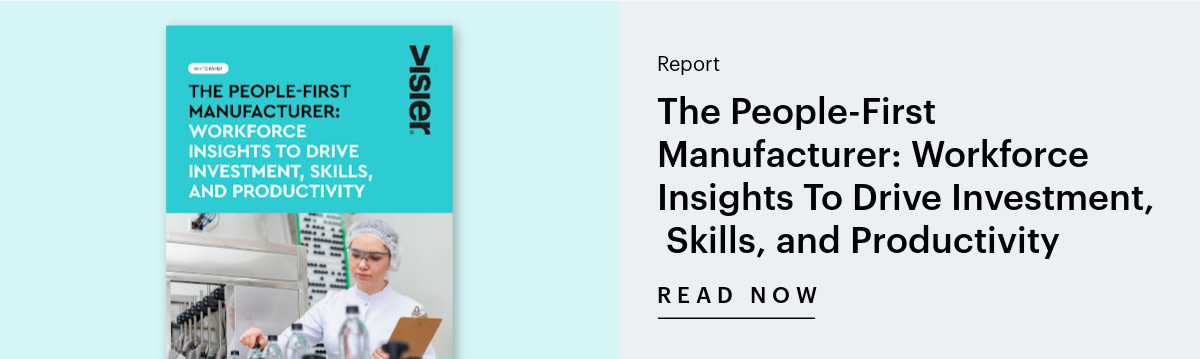
3. Build a resilient talent strategy in the face of uncertainty
From geopolitical instability to natural resource constraints, modern manufacturing operates in an unpredictable environment. In an increasingly volatile global economy, companies are seeing firsthand how vulnerable global supply chains can be. As a result, many are investing in local talent pipelines and supply chain diversification.
For example, Tesla explored taking a stake in commodities trader Glencore in an effort to bring some predictability to their supply of cobalt and lithium to make car batteries. With China controlling the majority of the global market for these materials, the electric vehicle manufacturer wanted to mitigate the risk an export ban would pose to its operations.
By using workforce analytics, manufacturers can identify shifts in talent, labor costs, and turnover and take data-driven actions to pivot quickly and stay competitive. For example, Sunstate Equipment, a construction equipment rental company, faced high turnover rates and escalating overtime costs, which adversely affected equipment utilization and revenue. By implementing Visier's workforce analytics solutions, Sunstate gained real-time insights into its workforce.
The team was able to use these insights to identify and address the root causes of turnover, leading to a 50% reduction in turnover rates and a 10% decrease in overtime. These improvements stabilized operations, enhanced productivity, and supported revenue growth.
"Connecting workforce analytics and financial information is crucial. With Visier, we can tell the whole story of how a metric like turnover impacts the bottom line very succinctly and accurately."
Sameer Raut, Vice President of HRIS, Sunstate Equipment
Talent is a top driver of value creation. Manufacturers that embrace workforce analytics as a strategic imperative will be better positioned to innovate, grow, and lead. Visier gives you the insights you need to build a resilient, high-performing team.
